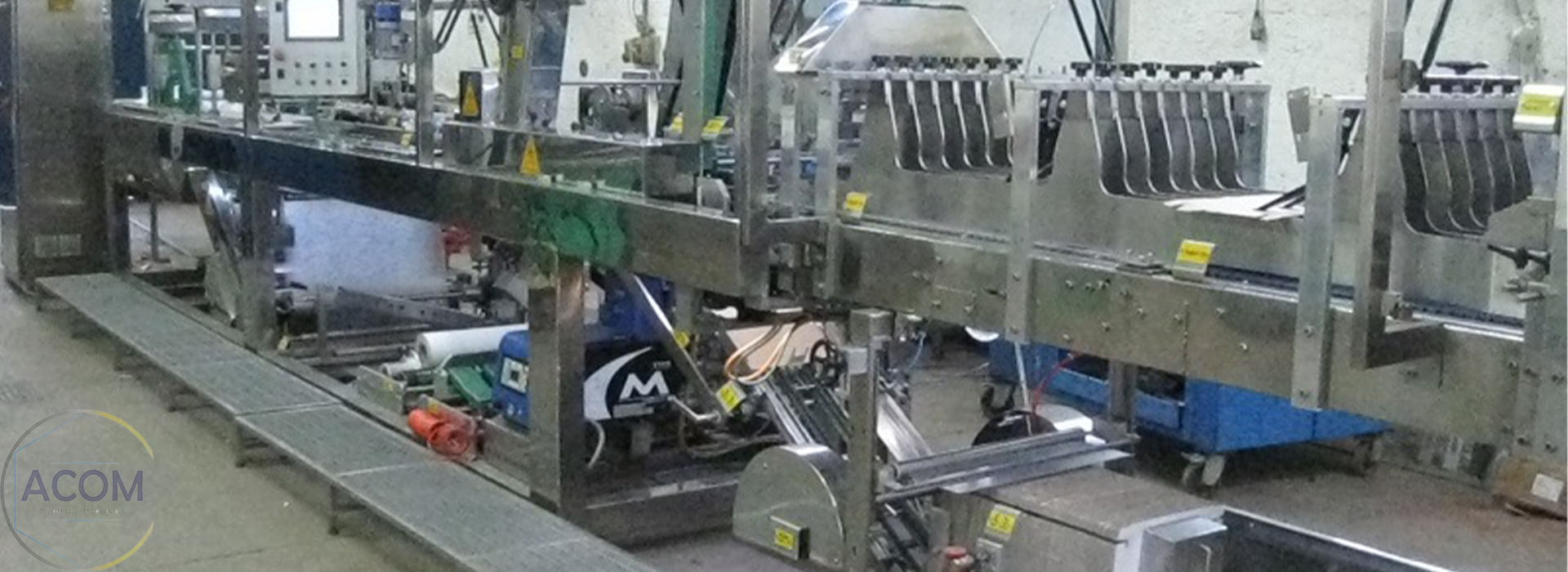
FARDELLATRICE IN TERMORETRAIBILE IN ACCIAIO INOX DOTATA DI ALIMENTAZIONE A BASSO IMPATTO PER LAVORARE VOSSI O FALDA PIANA
Il motore principale della macchina è gestito da un inverter che trasmette un segnale di riferimento da 0 a 10 volt. Questo segnale va a pilotare altri due inverter, il primo provvede al moto del tappeto in plastica in alimentazione, mentre il secondo la rete metallica di separazione e il sistema a nastri in plastica speciale che permettono la stabilità del prodotto nella fase di formazione del fardello. La velocità della rete metallica di separazione e dei nastri superiori viene mantenuta perfettamente uguale mediante un sistema di rinvio meccanico. Variando la velocità della macchina i due motori sopracitati varieranno di conseguenza. Le barre superiori (traversino) di compattazione e spinta del prodotto nella stazione di avvolgimento sono collegate meccanicamente al motore principale. Le barre per l’avvolgimento del film sul prodotto sono comandate da un asse elettrico di posizione* asservito da un motore brushless che prende il comando dall’econder assoluto montato sul motore principale della macchina (*Questo sistema per posizione, garantisce l’esatta corrispondenza per ogni grado d’avanzamento macchina). Il motore che comanda la rete del tunnel è comandato da un inverter che modifica la velocità della stessa in funzione della velocità della macchina e del formato in operazione in quel momento.
CICLO DI FUNZIONAMENTO MACCHINA
Il prodotto alimentato da un tappeto in plastica viene aiutato ad incanalarsi nelle varie guide grazie ad un sistema Disfaponte Oscillante con componente diagonale. Le scatole incanalate nelle guide vengono separate sfruttando il funzionamento ad intermittenza del Separatore a basso impatto, costituita da una rete metallica e un sistema per l’equilibrio del prodotto a nastri in plastica superiori. Le diversa velocità del tappeto in plastica in ingresso(<) rispetto alla velocità della sistema rete metallica e nastrini superiori (>) permette di poter lavorare anche prodotti estremamente fragili, in modo da avere basse soglie di rumore. Il prodotto separato viene compattato e trasferito nella zona d’avvolgimento mediante apposite barre (traversino). Nella fase d’attraversamento del prodotto dai traversini al dispositivo motorizzato a rulli di sincronizzazione con la rete tunnel, avviene la fase d’avvolgimento. Il sistema d’avvolgimento si suddivide in 4 fasi principali: 1. Il film prelevato direttamente dalla bobina (senza nastri sottovuoto di risalita film) viene accoppiato alla base del prodotto alla stessa velocità. 2. La barra d’avvolgimento con moto verticale verso l’alto determina la lunghezza del film. 3. Raggiunta la quota/lunghezza film desiderata la barra compie una sosta di 0.2” durante la quale avviene il taglio del film. 4. Avvenuto il taglio, la barra ad una velocità programmata in funzione del formato conclude l'avvolgimento prima del passaggio del prodotto. Tutte queste fasi sono pre programmate sull’elettronica di gestione ( PLC, Controllo assi).
PRESA CARTONE
Il cartone viene prelevato dal magazzino con un braccio meccanico dotato di ventose. Queste ultime sono asservite da generatori di vuoto (venturimetri). Il magazzino cartoni è regolabile ed ha una capienza di 700 cartoni. L'avanzamento degli stessi è assicurato da un nastro ad avanzamento passo-passo. Il cartone prelevato, viene depositato all'interno di un trasportatore a vani che lo farà accoppiare al prodotto.
FORMAZIONE VASSOIO
La formazione del vassoio avviene in continuo con sistema wrap-around. Il primo lembo viene ripiegato con l'arrivo del primo nasello della catena a vani; durante l'avanzamento del cartone viene caricato il prodotto in sincronia con l'avanzamento del cartone stesso. Successivamente viene ripiegato il lembo posteriore dai naselli della catena; segue la piegatura delle pattelle anteriori con contrasti fissi, mentre quelle posteriori vengono ripiegate con piegatori rotanti. A questo punto viene spruzzata la colla sulle patte laterali, le quali, sempre avanzando in continuo, vengono ripiegate con un'elica fissa. Il fardello avvolto viene avviato al tunnel di retrazione tramite la rulliera a rulli motorizzati/frizionati che consentono di armonizzare la velocità del nastro d’avvolgimento con quella della rete del tunnel. Nel tunnel di retrazione sono presenti deflettori per la gestione del flusso di aria calda sia nella parte inferiore della rete che nella camera di retrazione. All’uscita del tunnel il fardello viene raffreddato da soffianti poste nella parte superiore. L’intero ciclo della macchina è controllato da PLC e controllo assi. Tutte le fasi sono controllate da sensori, le eventuali anomalie nelle varie fasi macchina determinano un arresto della stessa e queste vengono evidenziati da allarmi sonori/luminosi e contemporaneamente appare sul display del pannello di comando il tipo d’anomalia e le operazioni necessarie al ripristino della macchina.
Immagini
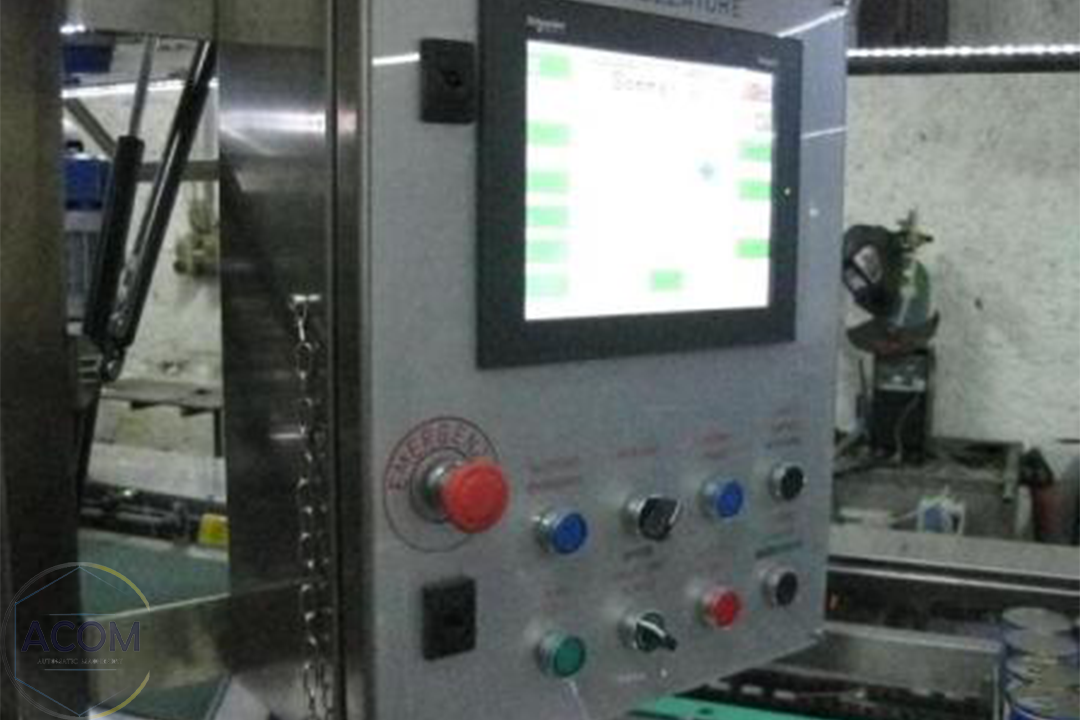
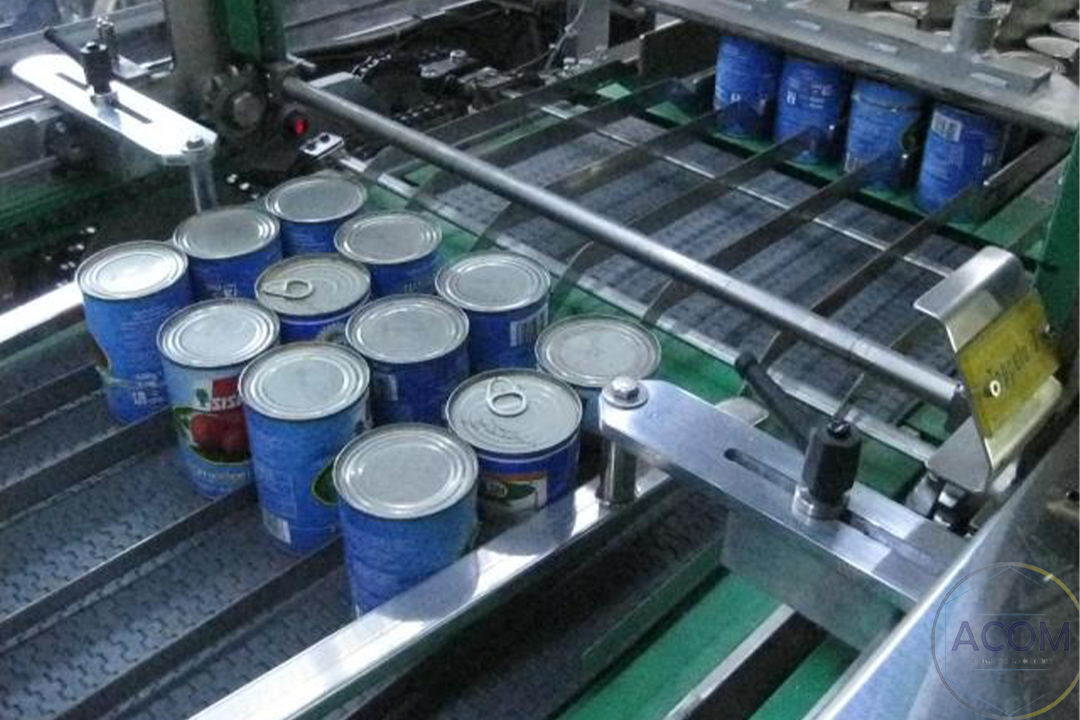
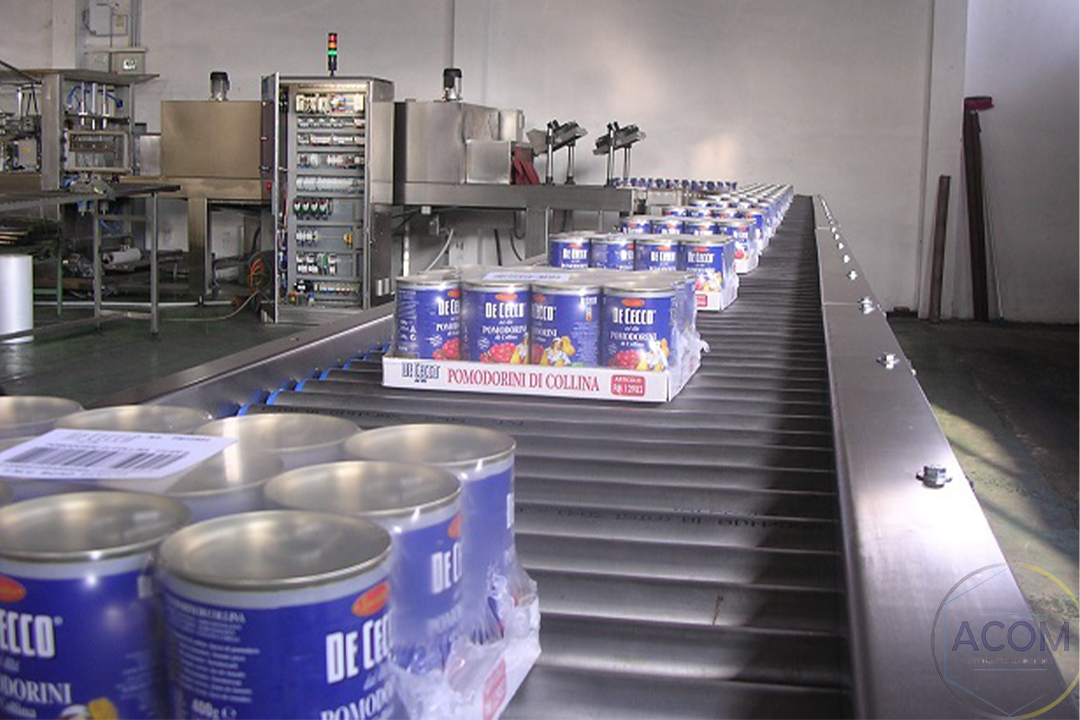
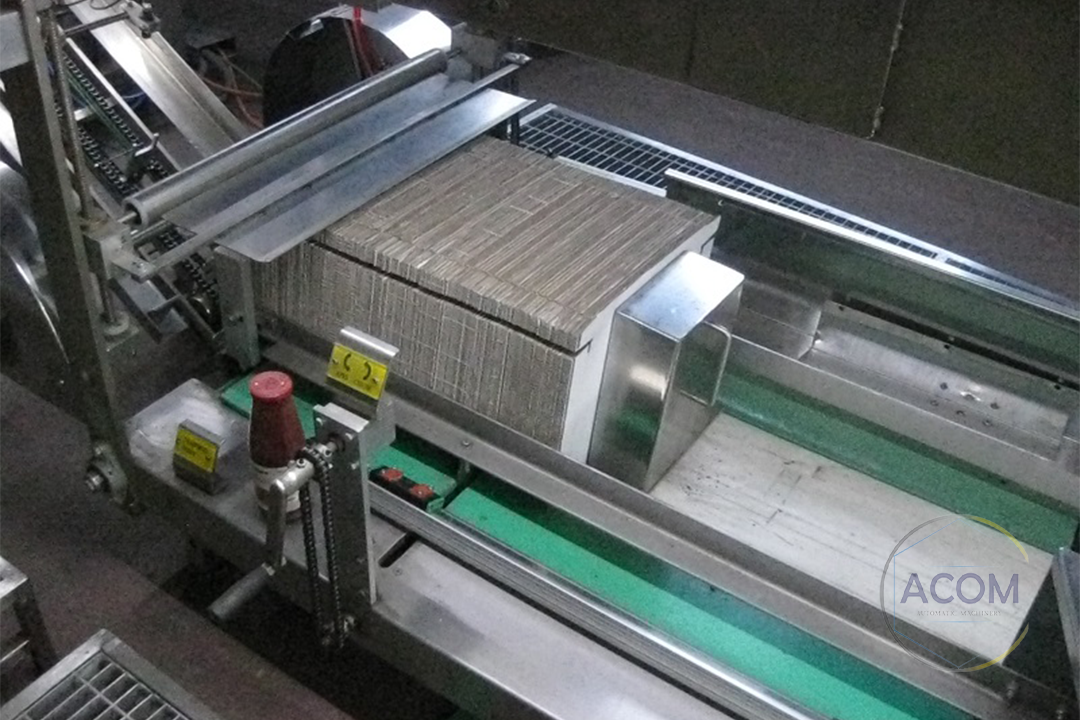
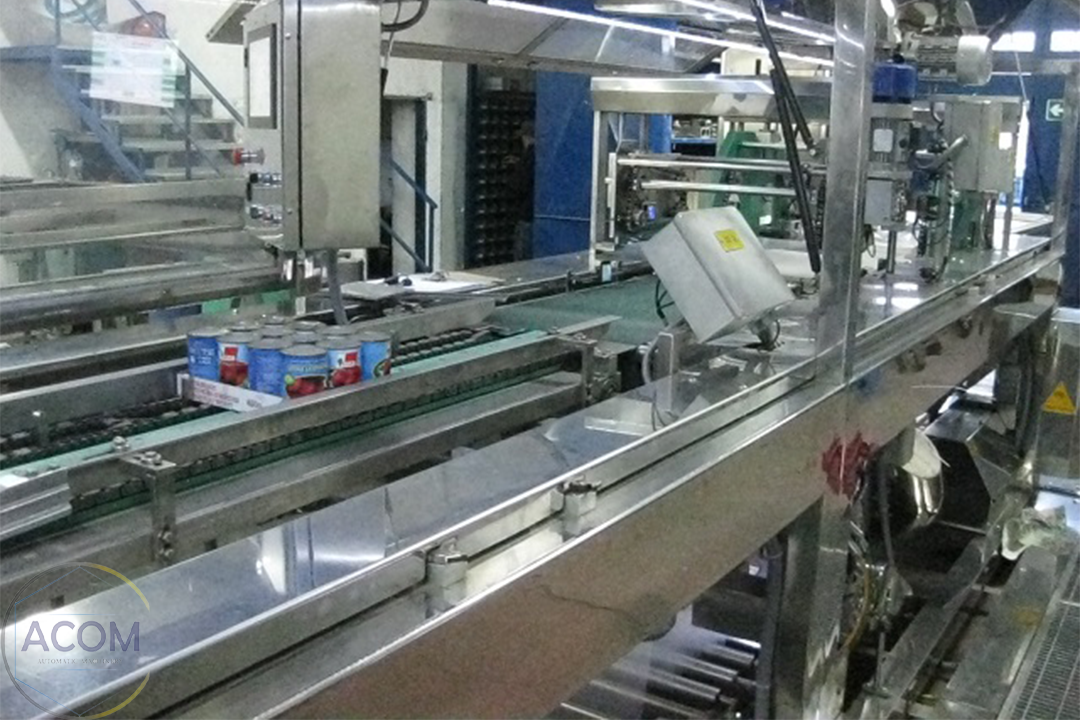
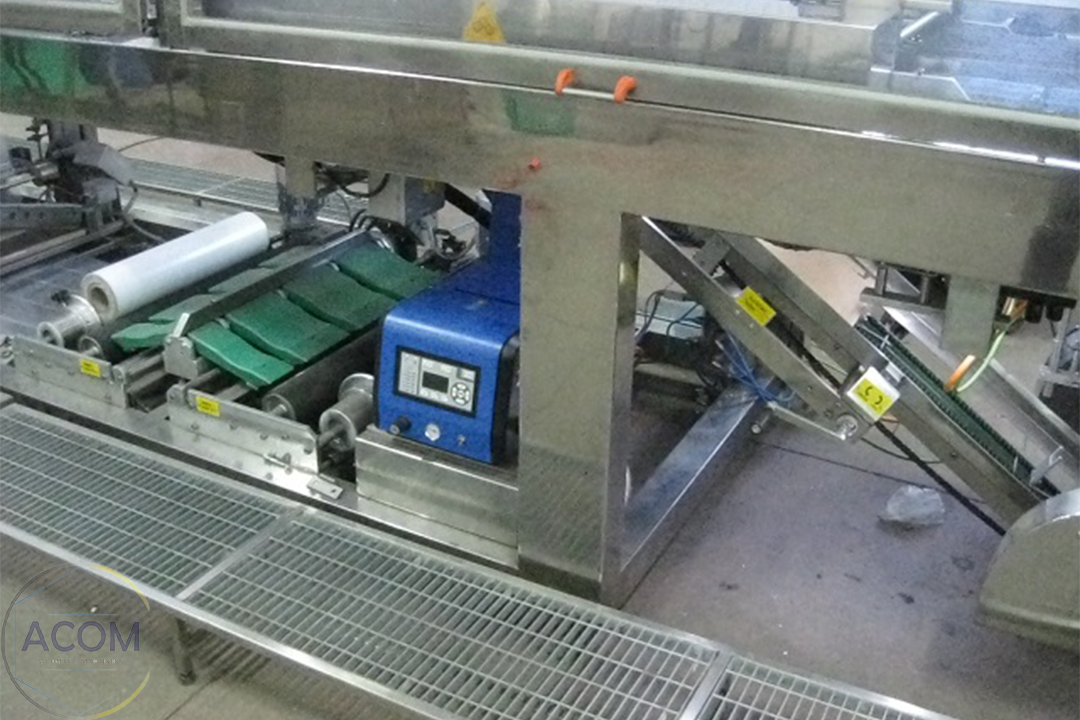
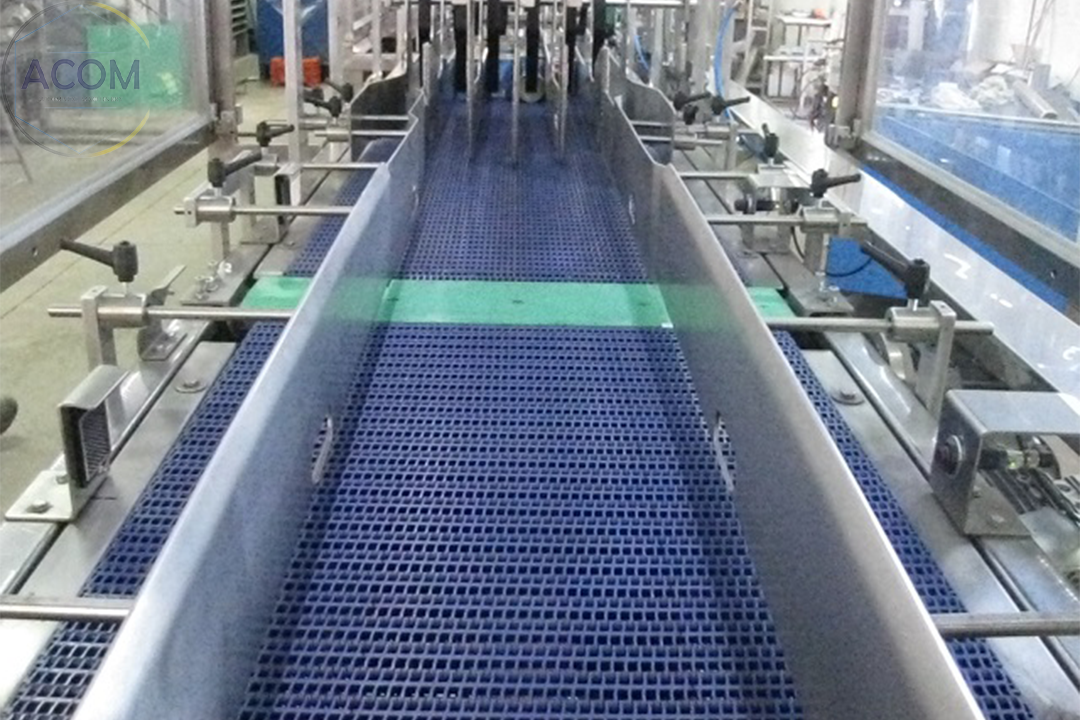
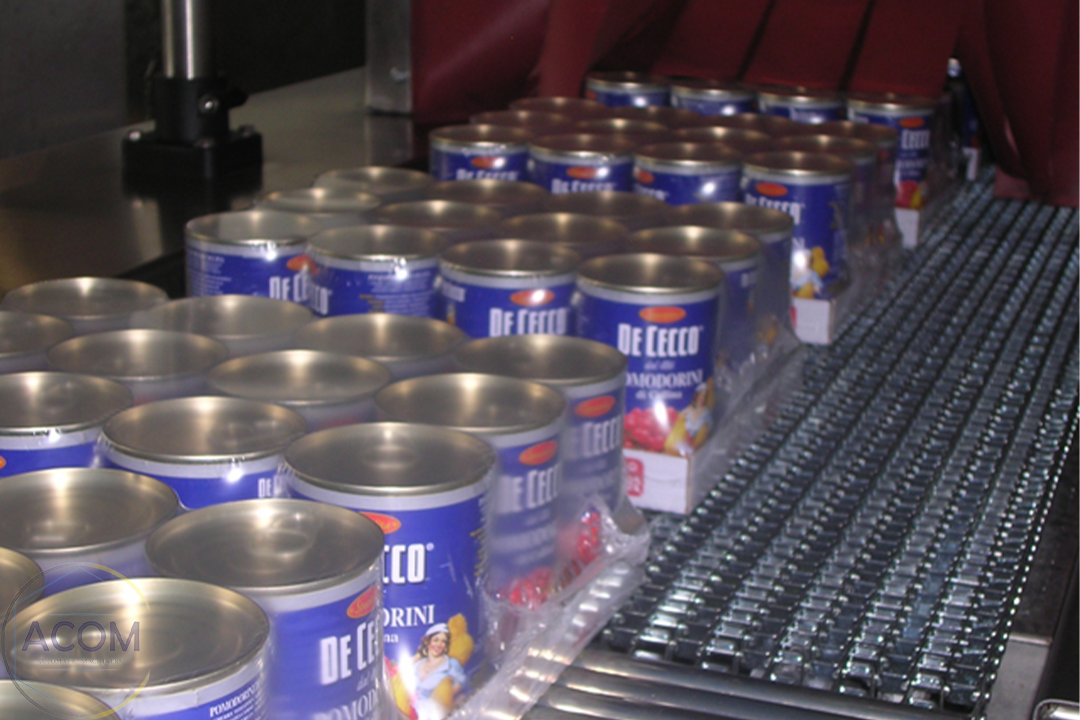
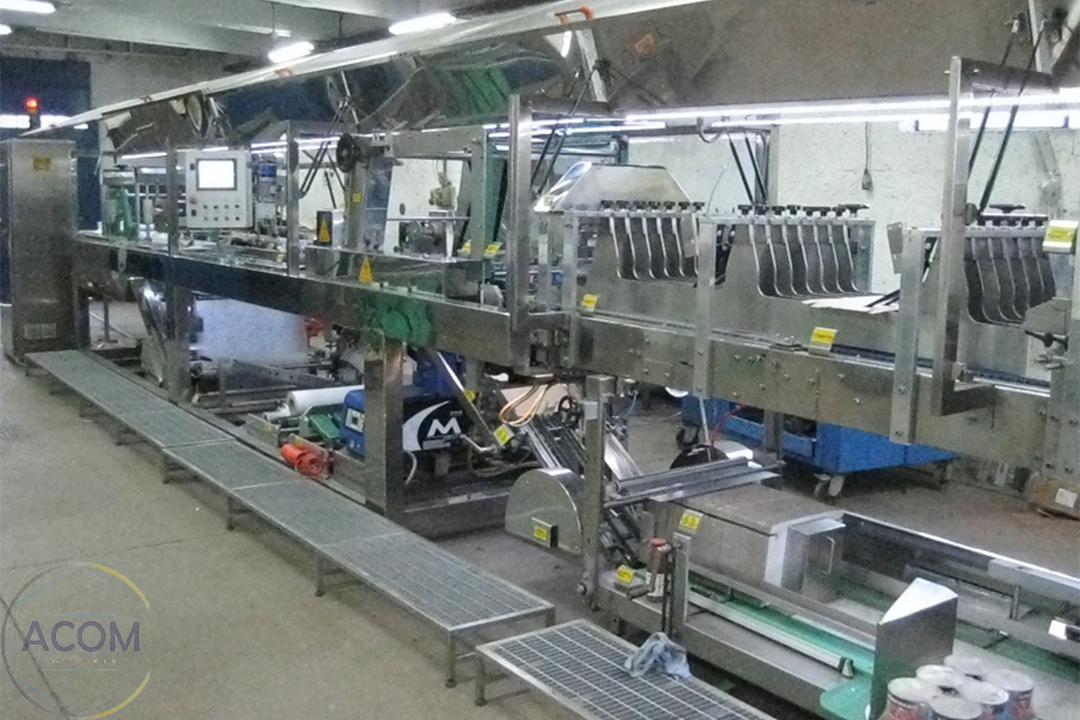
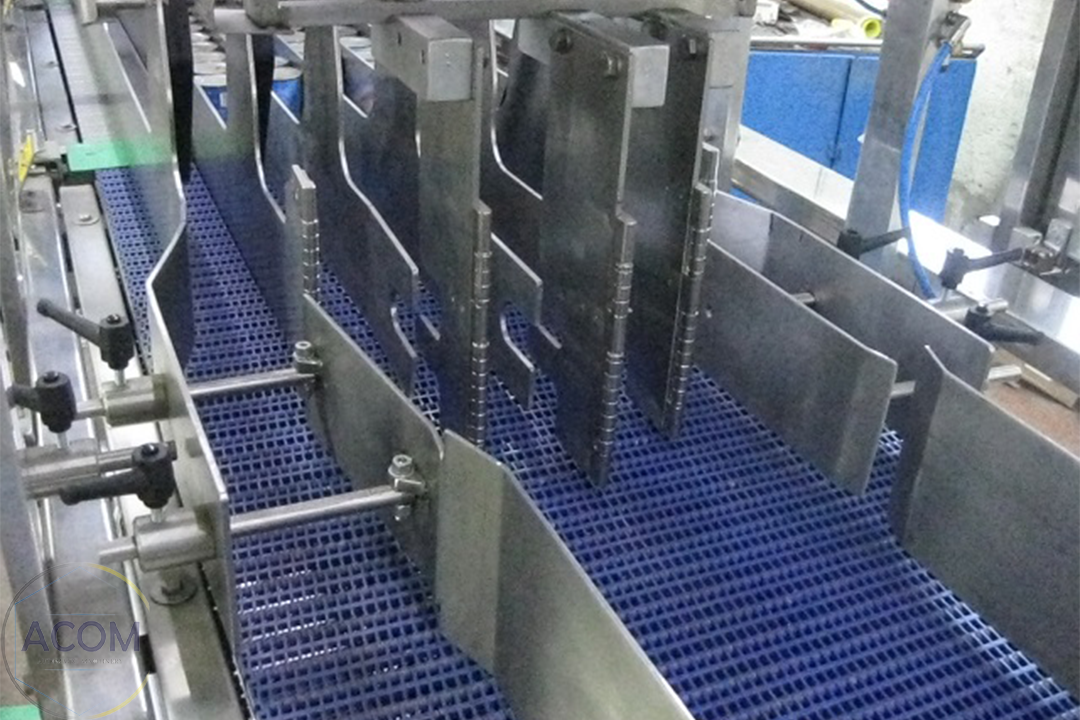
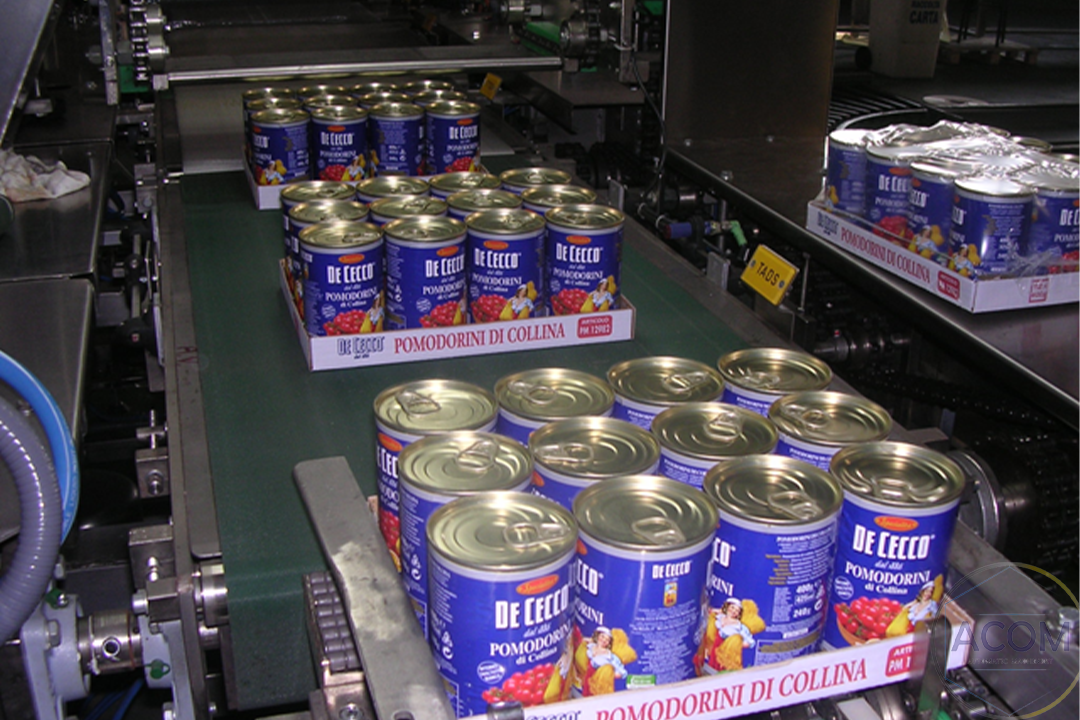
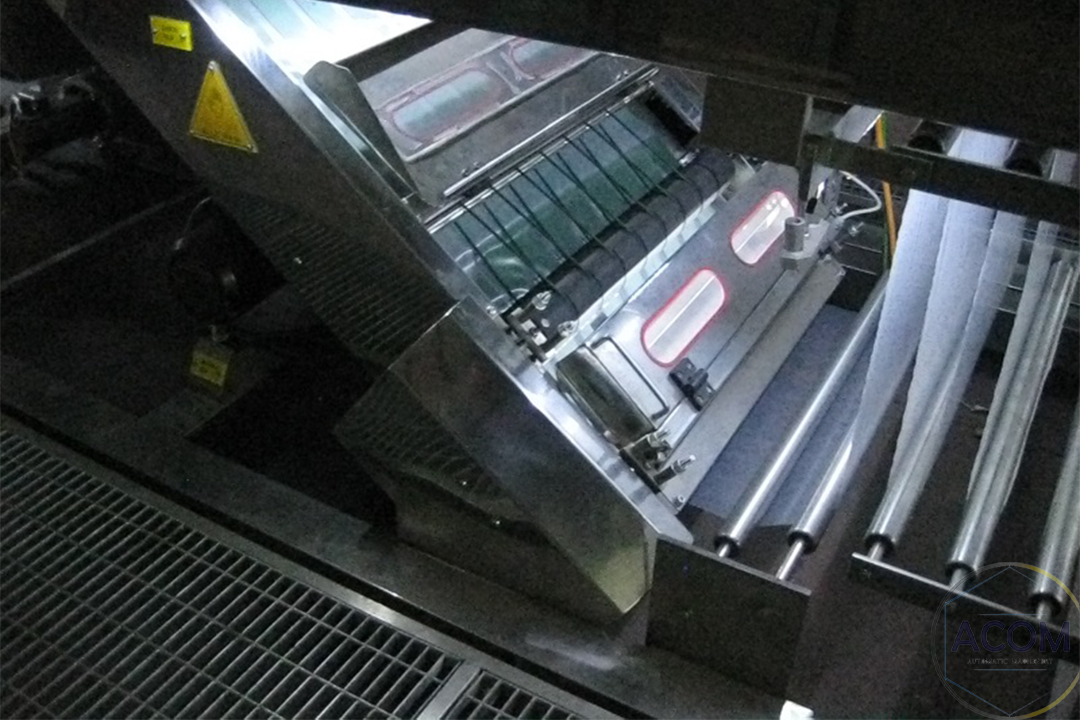